Galvanizing
In conditions defined as normal the best performance has been achieved in structural of structural steelwork with zinc coating. However, account should be taken that the value of zinc protection layer can be reduced in time due to various environmental influence on zinc. The warranty period is established upon the thickness of zinc layer, as well as yearly reduction value of protection layer in relation to various environmental influence on zinc acc. to the corrosion category and in conformity with the PN-EN ISO 12944-2/2001 standard.
Corrosion category
|
Reduction of Protective Layer
(µm) |
Examples of Environment in Temperate Climate (for information only)
|
C1
insignificant |
< 0,1
|
Indoor: heated buildings with clean atmosphere, e.g. shops, offices, etc. Outdoor: – |
C2
low |
> 0,1 to 0,7
|
Indoor: non-heated buildings with condensation, e.g. sports arenas, warehouses, etc. Outdoor: atmosphere with low level of pollution |
C3
medium |
> 0,7 to 2,1
|
Indoor: production facilities with increased humidity and moderate pollution, e.g. breweries, laundries, creameries and dairies, etc. Outdoor: urban and industrial atmosphere |
C4
high |
> 2,1 to 4,2
|
Indoor: chemical plants, swimming pools, shipyards Outdoor: industrial zones and inshore areas with moderate salinity |
C5
very high (industrial) |
> 4,2 to 8,4
|
Indoor: buildings or areas with permanent condensation and extreme pollution Outdoor: industrial zones with damp conditions and aggressive atmosphere |
C5-M
very high (marine) |
> 4,2 to 8,4
|
Indoor: buildings or areas with permanent condensation and extreme pollution Outdoor: inshore and offshore areas with intense salty atmosphere |
The required thickness of zinc coating can be measured by multiplying the value of annual reduction by the expected time of operation.
As the standard practice three methods of zinc coating are commonly used which differ in terms of the obtained protective zinc layer: Electro Galvanizing acc. to PN-EN 12329, Strip Galvanizing according to the Sendzimir Method, Mild Steel Hot-Dip Galvanizing.
Elektro Galvanizing acc. to PN-EN 12329
Small elements (bolts, nuts, washers) are covered with thin and uniform zinc coating in electrolytic bath, the coating is between 5 – 20 μm, color is bright and shiny.
Strip Galvanizing according to the Sendzimir Method
Elements intended for application in predominantly dry premises of C1 and C2 class, with zinc layer ca. 19 μm.
Mild Steel Hot-Dip Galvanizing
Elements intended for application in environments of the corrosivity class C1, C2, C3, C4, C5-I, C5-M , with average thickness of zinc layer between 45 μm – 55 μm.
Type of atmosphere | insignificant load | small load | moderate load | heavy load | extremely heavy load |
Corrosion aggressiveness category | C1 | C2 | C3 | C4 | C5-I, C5-M |
Corrosion aggressiveness category | up to 5 years | up to 5 years | up to 5 years | up to 5 years | up to 2 years |
Elements and thickness of elements
|
Local coating thickness (µm)
(minimum value) (µm) |
Average coating thickness
(minimum value) (µm) |
Steel >6 mm
|
70
|
85
|
Steel >3 mm to <6 mm
|
55
|
70
|
Steel >1,5 mm to <3 mm
|
45
|
55
|
Steel <1,5 mm
|
35
|
45
|
Thermal Diffusion Galvanizing acc. to PN-EN 12329
In temperature of 360 – 450 °C the elements are coated with mixture of powdered zinc. Through permeation (diffusion) of zinc particles to the steel material a very sturdy anticorrosive layer is obtained, and, unlike in any other zinc coating a matt surface is achieved, from light grey to dark grey. The thickness of zinc coating is between 45 μm and 120 μm.
Zinc Flake Coating acc. to PN-EN ISO 10683:2014-09
In this technology the base coating is a kind of lacquer layer consisting of zinc flakes and aluminum. The obtained structure interacts with the steel surface and since it becomes heated up the adhesive, conductive and non-toxic zinc-aluminum coating is produced. The above method provides extremely high corrosion resistance up to 1000 hours in salt spray chamber acc. to ISO 9227, until red corrosion appears. Zinc Flake Coating has been commonly accepted method in the car, energy and aviation industry and is often used in manufacturing of threaded components as they can be screwed easily.
Powder Coating
Coating with polyester and epoxy powder (indoor application), with the coating thickness between 60 μm – 120 μm. Paint is applied directly to steel surface without use of primers and solvents. Coating obtained through powder painting produce surface which is smooth, free of cracks, stains or wrinkles. It is characterized by high resistance against corrosion, chemicals and water, and it has excellent mechanical properties. Such coating is applied in places where increased anticorrosion resistance is required (through powder painting onto the steel sheet), to improve appearance of any interior by using appropriate and consistent range of colors, and to identify the installation accordingly to its function and destination. The coating durability may vary and depends on the following factors: obeying the rules of transport, storing conditions, method of installation, chemical environment in which the steelwork has been assembled and maintained. 14 colors are offered in the standard range (see the color palette below). Custom colors can be ordered, however at the increased price of service provided and with extended time of delivery.

Stainless Steel and Acid-Resistant Steel
Steel sheet for general-purpose applications with sufficient resistance to atmospheric corrosion and variety of organic and inorganic chemical substances acc. to PN-EN 10088, in the following grades:
1.4301 (304) used for production of milk tanks, dairy equipment, installations for production of milk, beer kegs, beer storage tanks at breweries, for beer fermentation, in corn products refining, as equipment for nuclear power plants, gutters, discharge pipes, tanks for liquid oxygen, hydrogen, nitrogen, as the elements of dispenser for carbonation of beverages, cryogenic plates and elements, furniture, tanks, siding for indoor and outdoor application.
1.4404 (316L)white wine tanks, brewing industry, paper and pharmaceutical industry, in production of fatty AIDS, acetic acid compounds, for production of devices which are in contact with fertilizers, kettles for ketchup cooking, in phosphate fertilizers industry, as equipment in film processing, chimneys, tanks at water softening stations, pipes for yeast production, in marine environment.
1.4571 (316Ti) used in the chemical industry for production of equipment and devices with high resistance against corrosion, e.g. coolers, capacitors, pipelines, tanks; in the food, pulp and pharmaceutical industry.
Aluminum PN-EN 485-2
Resistant to atmospheric corrosion and variety of organic and inorganic chemical substances.
E30, E90 Systems, acc. to DIN 4102-12
The Ordinance by the Minister of Infrastructure dated 12 April 2012 on technical conditions of buildings and their location (Journal of Acts of 2002, No. 75, item 690), as amended on 12 March 2009, in § 187, point 3, provides as follows: ”Electric wires and cables, fiber optic cables and their fixings hereinafter referred to as the cable systems used in the power supply systems and in systems for control of fire protection devices shall assure continuous supply of electric energy or signal transmission for the period of time required to start-up and operate the device.”
In Poland there are no detailed guidelines and standards which regulate the requirements in relation to the products, the test methods have not been regulated or the authorized bodies appointed. In Europe, (also in Poland), the commonly applied and detailed standard for regulation of this issue is the German Standard DIN 4102:12. By Ordinance of the Minister of Infrastructure it is however required that the electric devices applied to save people’s lives in case of fire, such as emergency lighting, voice alarm systems, ventilators, elevators, pumps for supply of water to the sprinklers, ventilation flaps, etc., shall be provided with uninterrupted supply of electric energy or signal transmission for at least 30 minutes or 90 minutes in order to secure safe evacuation of people from the building under fire. According to the DIN 4102:12 standard developed by the Insitutes in Germany and based on many-year experience and tests carried out in the field of maintenance of functional integrity in electric installations under fire in construction industry such systems are commonly known and recognized as ,,E90” systems.
The basic assumption of the above mentioned standard is verification if the conduits, cables and fixings within the particular system guarantee electric energy supply to the life-saving devices under fire.
To date more than 60 tests have been carried out by the BAKS company with own products and cables of the following cable manufacturers: Bitner, Dätwyler, Elkond, Elpar, Eupen, Facab Lynen, Kabtek, Madex, Nexans, NKT, Prakab, Studer, Technokabel, TELE-FONIKA Kable. All the tests confirmed by respective certificates were carried out at the following accredited institutes: DMT Dortmund, Fires Batizovce.
Note!
To date the tests have been carried out with the following cable manufactures: Bitner, Dätwyler, Elkond, Eupen, Facab Lynen, Madex, Kabtek, Nexans, NKT, Prakab, Studer, Technokabel, TELE-FONIKA Kable.
Functional Integrity Maintenance Systems E-30, E-90
As the key issue today is the safety of people in public facilities all applied safety systems should be absolutely reliable. To meet new safety requirements the BAKS company embarked on a programme to test a new system of Ladders and Cable Trays which is entirely compliant with the DIN 4102, Part 12, Standard.
The basic assumption of the above mentioned standard is practical testing of cables and fixings named together as the ,,cable system”. The purpose of the tests is to verify if in required temperature and for the specified period of time electric energy has been continuously supplied to the equipment and devices. In order to assure uninterrupted supply of electric energy to such equipment and devices under fire the tests must be carried out of the cable route system with all cables applied.
Maintenance of electric installation functioning means continuous supply of electric energy to the building under fire. It does not refer to the electric installation in the building as a whole but only to those electrical circuits which are essential for the safety of people staying there. The typical examples of such circuits are emergency lighting circuit, voice alarm systems (DSO), ventilation devices in hotels, hospitals and public facilities. The above mentioned standard applies to the voltage up to 1kV. The DIN standard provides another group in E60 system, however it has been seldom used and applied. The capability to maintain functional integrity has been generally classified and assigned to 2 of the groups, in E-30 and E-90 systems.
Numerous tests have been carried out by the BAKS company at the accredited research institutes in Germany and Slovakia. The above mentioned tests were performed on the ceilings of aerated concrete, and B-20 concrete. The basis for the test carried out acc. DIN 4102 and in line with the commonly accepted practice the elements subject to testing are mounted in a furnace. The test is carried out according to the internationally approved method of measurement- temperature-time curve.
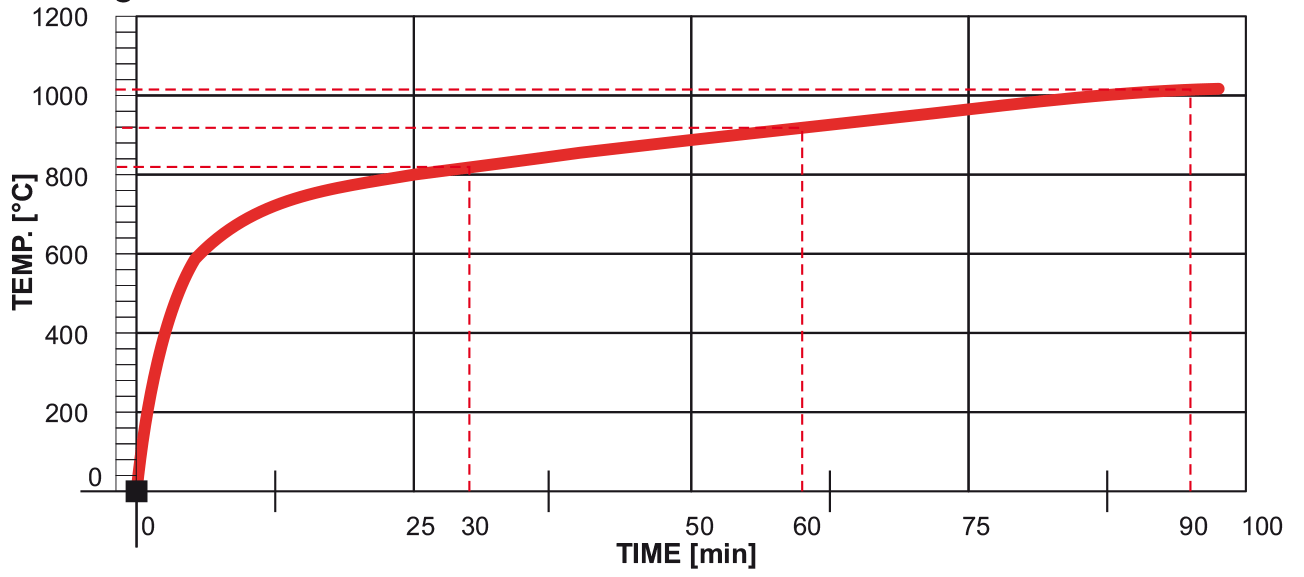
Cable Carrying Systems offered by BAKS and compliant with DIN 4102, Part 12, can be applied in variety of applications, i.e. as ceiling-mounted cable ladders, wall- mounted cable trays, fire resistant cables mounted to ceiling horizontally or wall-mounted vertically with a clamp or ladders. All systems can be manufactured in several available versions so the installer has an option to choose the most appropriate system to meet any specific requirements at the construction site
E-90 Tests
The photos from tests of the BAKS cable systems with cables of selected cable manufacturers in E-30, E-90 fire resistance systems. The tests were carried out at the following accredited institutes: DMT Dortmund, Fires Batizovce, MPA Braunschweig.